
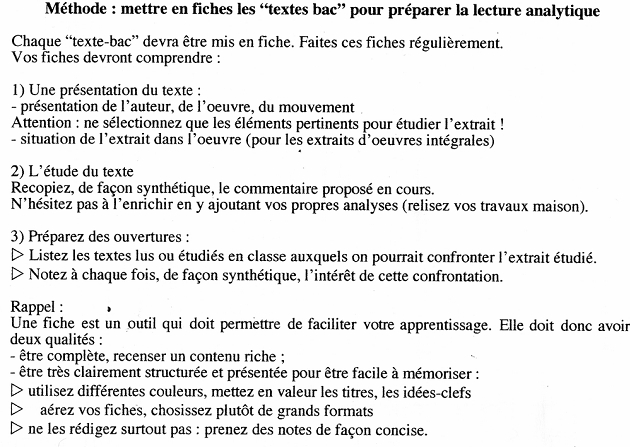
STL is a common file format and supported by most CAD software. Import the geometry of the blade model from an STL file. After defining the analysis type, we begin with the first step of the analysis. In a typical finite element analysis workflow, we go through four steps. We will be using the model object later on to set up the analysis. The PDE Toolbox supports various other types of analysis, such as transient, mortal, etc. We then specify the model to be a static solid model. To perform a structural analysis, we indicate that as the first argument. We start by creating a PDE model object that determines the type of analysis we're performing using the create PDE command. Let's now see how we can do this in MATLAB.
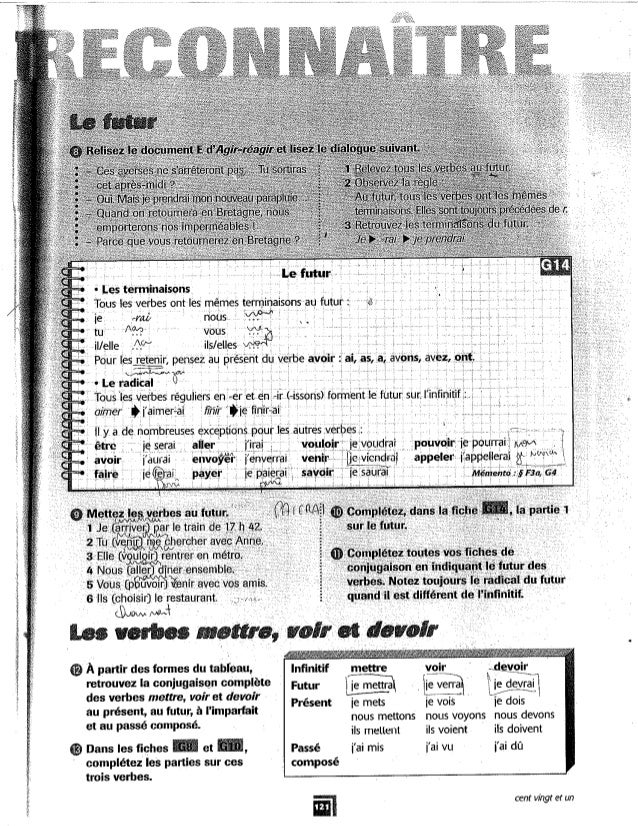
To avoid mechanical failure and friction between the tip of the blade and the turbine casing, the blade design must account for distress and the deformations. The blade material both expands and deforms significantly, producing mechanical stress in the joints and significant deformations of several millimeters. The turbine blades are surrounded by gases under extremely high temperatures and pressures.
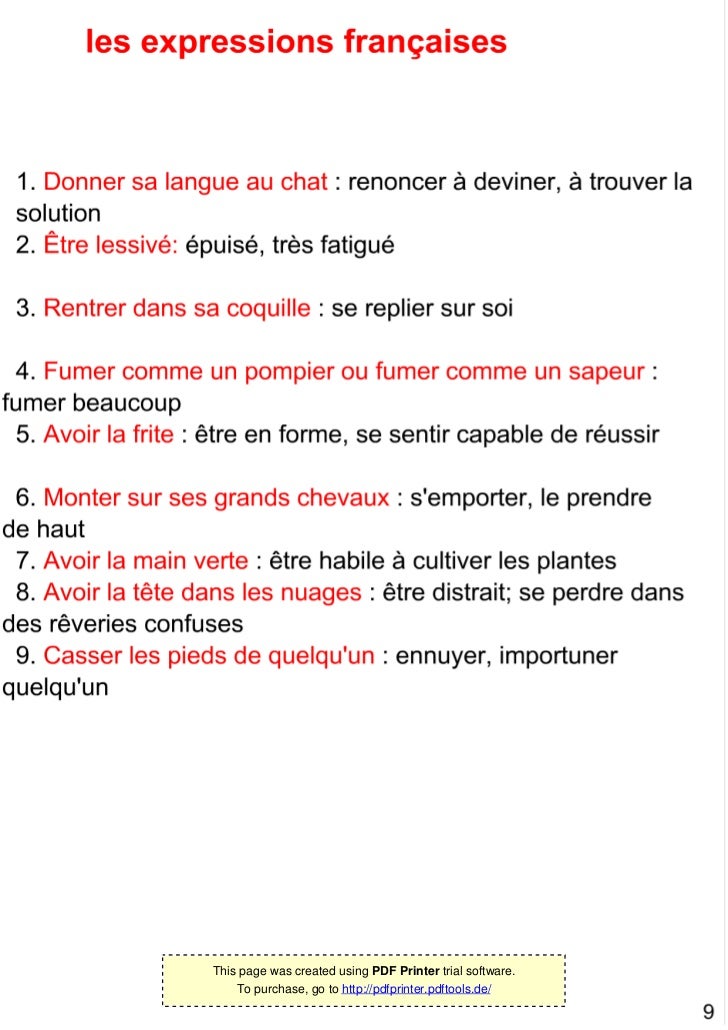
Within a jet engine, the turbine, a radial array of blades extracts energy from the high temperature and high-pressure gas produced in the combustion chamber and transforms it into rotational motion to produce thrust. But first what is a jet turbine blade? The jet engine on a plane is responsible for generating the thrust that enables the plane to fly. In this video, we will focus on performing structural analysis of the turbine blade that is subjected to pressure from the surrounding gases. The partial differential equations can represent physical problems ranging from simple cantilever deformation, heat dissipation in a motherboard to thermo-mechanical stress of a jet turbine blade.
#Methode de franais avec transcription pisode 1 how to#
In this video you will learn how to perform structural analysis using finite element method with partial differential equation toolbox in MATLAB.
